Reverse Engineering Vehicle PCB Board to Improve Vibration Capability
Another cause of reliability issues in vehicles is the constant vibration of the PCB and subsequent failure of component leads and accessories. Through Reverse Engineering Vehicle PCB Board to Improve Vibration Capability is one of the possible way, failures can generally be detected by building PCBA prototypes and placing them in an acceleration chamber, subjecting the PCB to vibration and temperature cycling.
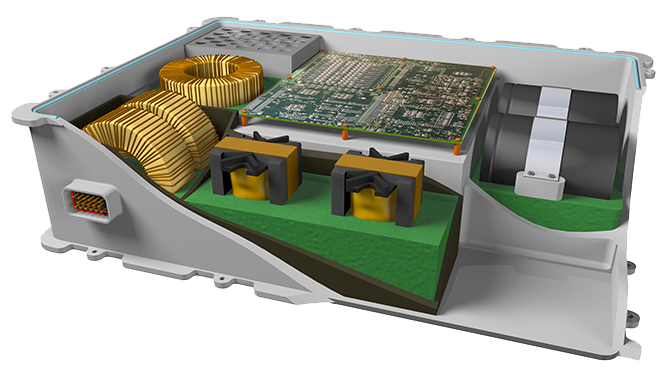
This approach requires building multiple electronic printed circuit board prototypes as the layout and schematic design reverse engineering progresses, and often takes weeks or even months to complete a simulation of the life expectancy of an auto component in an acceleration chamber.
This is a very time-consuming and expensive process, so reliability enhancement testing may not be complete and comprehensive. Software is currently available to perform the same tests in virtual prototyping mode.
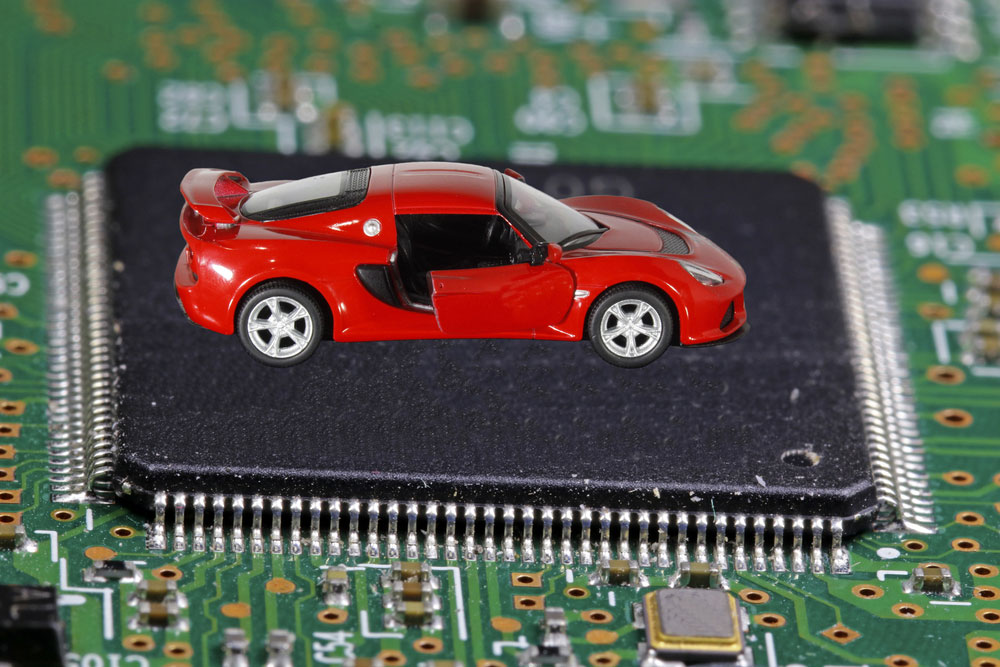
Designers can use this software to define the automotive electronic PCB board reliability and easily conduct loss simulation experiments. The software can perform complex analyses in a few hours and point out possible failures. These faults can be corrected and the simulation rerun in a new design version.
This iterative process can quickly lead to a suitable reliability solution. The Israeli Ministry of Defense had early success deploying the software on their new generation of combat vehicles;